Нож своими руками из полотна. Как сделать нож в домашних условиях. Как сделать нож своими руками из полотна. Нож из полотна пилы. Нож своими руками. Материал для клинка: ровная и плоская заготовка, ножи газонокосилки или старые напильники. Судя по опыту именитых ножовщиков, самое сложное - углубиться и начать. Самая сложная часть любого проекта, когда-либо осуществленного, заключалась в принятии самого решения о начале работы. Когда же начало положено, остается лишь преодолевать проблемы и не сдаваться. Величайший изобретатель Томас Эдисон как-то писал: «Неудачниками становились те люди, которые не понимали, насколько они были близки к успеху, когда сдались».
Существуют некоторые устоявшиеся соображения по поводу того, как должен начать свою работу новоиспеченный ножовщик.
Рекомендуется изготавливать первые ножи с помощью простых и даже временно приспособленных инструментов. Так вы сможете приступить к ножевому производству без больших затрат. Если такой простой метод вам не подходит, хватайте чековую книжку и кредитные карточки и отправляйтесь в магазин. И не забудьте список основных инструментов.
Статьи о изготовление ножей своими руками Смотреть
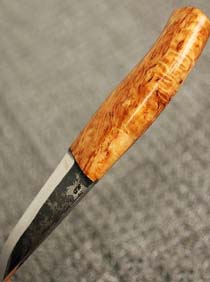
Рукоятку ножа из бересты Смотреть статью
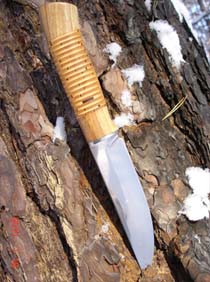
Из чего сделать ручку на нож Смотреть статьи
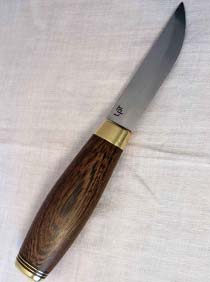
Ножны своими руками из кожи Смотреть статьи
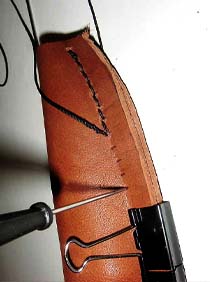
Из чего сделать нож в домашних условиях Смотреть статью
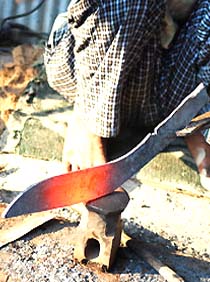
Дизайн повседневного рабочего ножа
С точки зрения конструкции дизайн нашего проектного ножа простой и практичный. Несмотря на свою простоту, нож очень полезен в работе. История на нашей стороне, так как именно простым рабочим ножом человек добывал себе для пропитания мясо животных. Люди, жившие близко к земле, выполняли таким ножом множество других функций. Им не требовались замысловатые дизайны или красивая полировка. Все, что им было нужно, — это острый клинок и надежная рукоятка.
Говорят, что совершенный дизайн получается тогда, когда все лишнее убрано. Поэтому наш проектный нож также лишен замысловатой обработки напильником, золоченых вставок, дополнительной гарды, черенков или навершия. Он имеет только то, что необходимо для выполнения работы.
Форма его клинка известна как «приспущенное острие». Еще ее называют утилитарной формой. Если вы посмотрите значение слова «утилитарный» в словаре, то найдете там что-то типа «качество, необходимое для практического использования». Приспущенное острие имеет множество преимуществ по сравнению с приподнятым острием на некоторых промышленных ножах или ножах ручной работы.
Есть мнение, что приподнятое острие пришло к нам из эры ножей Боуи. Приспущенное острие не только прочнее, но и более удобно для выполнения практически любой работы, которую только можно себе представить. И можно вспарывать шкуру охотничьих трофеев, не заглубляя клинок слишком глубоко. Когда дело доходит до свежевания или разделки туши, приспущенное острие или его незначительная модификация, известная как полусвежеватель, не знает себе равных.
Гарда проектного ножа является интегральной частью рукоятки — гарда и рукоятка представляют собой цельную деталь, и это упрощает конструкцию. Она обеспечивает безопасность, не позволяя пальцам пользователя соскользнуть на лезвие.

Проектный нож с утилитарным клинком показан также с клинком в стиле полусвежеватель, но оба ножа имеют аналогичную базовую форму рукоятки.
Два клинка отличаются только острием. Обратите внимание на различный вид этих двух рукояток
Однако, думать, что вы не обрежетесь своим ножом, если у него будет гарда, все равно, что надеяться, что вы не попадете в аварию, если никогда не будете отстегивать ремень безопасности.
Материалы рукоятки
Современный охотничий нож должен быть долговечным. Первоклассные красивые материалы для рукоятки могут увеличить стоимость ножа, но ваши затраты будут оправданы.
Рукоятка современного ножа должна быть выполнена из материала на пластиковой основе. Такие материалы водостойкие, прочные и надежные. В конечном счете заточка изнашивает клинок, но из многочисленных сред, которые воздействуют на натуральные материалы рукоятки разрушительно, лишь немногие могут повлиять на микарту. Нож из нержавеющей стали с рукояткой из микарты переживет своего владельца. Микарта, относится к семье термопластиков и состоит из пары дюжин различных типов материалов.
Традиционно материалы рукояток в определенной степени зависят от страны происхождения. Дерево, слоновая кость, рог, рога оленя и кость до сих пор используются для изготовления рукояток.
Недостаток таких естественных материалов состоит в том, что они легко царапаются, подвергаются нападению жучков или страдают от зубов животных. Естественные материалы имеют свойство впитывать влагу, когда намокают, и сжиматься, а порой и трескаться, когда высыхают.
Сегодня существует тенденция использовать выдержанное дерево. Дерево можно окрасить практически в любой цвет и затем выдержать. Заготовки из твердых пород дерева следует вырезать чуть больше проектных размеров законченной рукоятки, а затем хранить в сухом месте минимум шесть месяцев, а лучше год. Дерево в центре бруска 5,08 x 10,16 сантиметров будет иметь большую влажность, чем крайние слои.
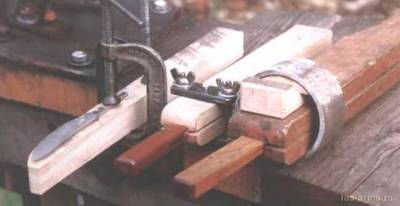
Вот три примитивных способа закрепления ножей. Слева простая доска для ножа. Зажим с силой удерживает клинок.
В центре тиски для ножа, изобретенные Джином Чепманом.
Справа сложные тиски для ножа, изобретенные автором В них используется сила клина.
Обычно необходимо проверять содержание влаги эбенового дерева, взвешивая небольшой кусок (кубик примерно в полтора сантиметра) на весах для отмеривания пороха при зарядке патронов.
Карандашом записывается вес на тестируемом куске, а затем он помещается под лампу, которой просушивается эпоксидный клей. Температура светильника устанавливается примерно на 50 градусов по Цельсию.
Этот образец взвешивается каждые 4—6 часов, пока он не перестанет терять в весе. Так можно узнать, сколько влаги дерево должно отдать. На этом этапе материал суше, чем должен быть. Если закрепить его на ноже в таком дегидрированном состоянии, то он может разбухнуть в условиях нормальной средней влажности и температуры своего нового дома.
В работе необходимо использовать материал средней влажности (5 – 8 %), и тогда, если повезет, он сохранит примерно те же размеры и останется плотно фиксированным к хвостовику ножа. Правильно выдержанное дерево решает эту проблему.
Проект ножа
Наш проект состоит в изготовлении повседневного рабочего ножа. Тип ножа, который мы решим иметь при себе для повседневной работы, зависит от нашего опыта и типа выполняемой работы. Главный принцип состоит в том, что, когда дело касается реальной работы, любой нож лучше, чем его отсутствие.
У проектного ножа будет узкий хвостовик и две накладки рукоятки с вырезом для помещения хвостовика. Рукоятка не будет оснащена дополнительной гардой и может быть изготовлена только ручными инструментами.
Оборудование мастерской
Не ждите, пока у вас появится идеальная мастерская. Идея заключается в том, чтобы начать с того, что у вас уже есть. Вы можете делать ножи, даже если у вас есть только острый карманный нож и несколько кусков мягкого дерева. Воспользуйтесь вышеописанным методом создания дизайна, начертите планируемый вами нож на куске дерева, а затем вырежьте нужную форму.
В ходе работы вы научитесь самостоятельно усматривать симметрию в куске материала, научитесь придавать поверхности рукоятки красивый радиус.
Возможно, вы не планируете стать резчиком по дереву, но это упражнение послужит началом вашего становления как ножовщика. Вдобавок вы получите практику заточки ножей.
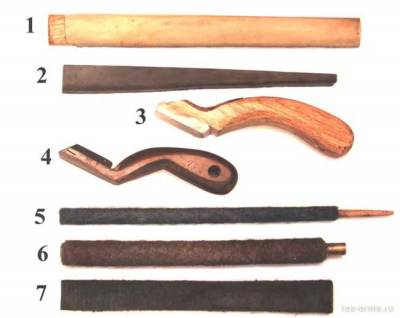
Это толкательные стержни для обработки ножа наждаком. Обратите внимание на различные типы этих стержней.
Каждый предназначен для конкретного вида работы.
Для начала работы вам будет достаточно тех инструментов, которые обычно можно найти в домашней мастерской: верстачный шлифовальный станок, дрель и тиски. Абразивное режущее колесо на шлифовальном станке или самодельный шлифовальный станок позволят вам сэкономить много времени по сравнению с резкой стали ножовкой вручную. Вам также потребуется какой-то верстак.
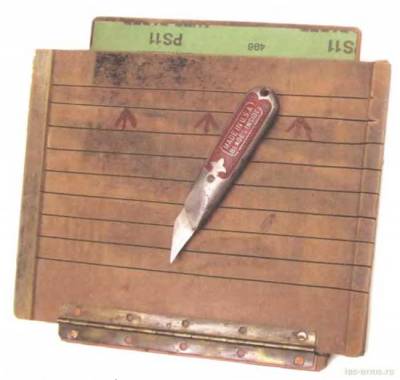
Шаблон для резки наждачной бумаги 8 на 8 дюймов позволяет разрезать цельный квадратный лист на полоски по одному дюйму.
Теперь вам нужно подобрать следующие инструменты:
Защитные очки или маска.
Бумажный или люксовый респиратор от пыли. Любая защита лучше, чем ничего.
Купленный или самодельный шлифовальный станок, угловой шлифовальный станок либо любой другой, который вы сможете найти.
Сверлильный станок, электрический или ручной, с набором сверл, соответствующих размеру заклепок.
Гибкая дисковая насадка для наждака с деревянным и металлическим рабочими дисками. Ищите те, которые работают с дисками, приклеивающимися тыльной стороной.
Тиски с мягкими вставками на губах.
Пропановая горелка.
Выдерживающие высокую температуру мягкие огнеупорные кирпичи для изготовления кузнечного горна из одного кирпича.
Напильник по стали.
Любой рашпиль для грубой обработки деревянных рукояток.
Одна-две струбцины.
Чертилка для разметки металла (ее можно сделать из старого треугольного или круглого напильника.
Кернер.
Экономную печь-тостер с точным термометром.
Выдвижной магнит из дешевого магазина.
Точильный камень. Если его нет, подойдет влажная или сухая наждачная бумага.
Гибкая дисковая насадка для наждачной бумаги с набором дисков.
Молоток со сферическим бойком.
Подберите следующие материалы:
1 4 - 8 литров масла для закалки клинка. Еще его называют паста для закалки. Для этого подойдет использованное моторное масло, пищевое масло, жир, оставшийся на кухне, масло для автоматической трансмиссии или гидравлическое масло. Различные смеси некоторых или всех этих масел и жиров тоже подойдут. Эти масла и жиры следует держать в металлическом контейнере с крышкой, чтобы можно было легко погасить любое их воспламенение. Рекомендуемая паста для закалки клинка проектного ножа на треть состоит из жира, оставшегося на кухне, на треть из парафина и на треть из гидравлического масла или жидкости для автоматической трансмиссии.
2 Материал для клинка: ровная и плоская заготовка, ножи газонокосилки или старые напильники.
3 Материал для рукоятки: дерево или микарта.
4 Грубая, средняя и тонкая наждачная бумага.
5 Эпоксидная смола DuroQuick Set.
6 Тонкая спрессованная стальная стружка для шлифовки.
7 Ножевая доска, изготовленная из куска твердого дерева, толщиной 3/4 дюйма, шириной 5,08 сантиметров и длиной 30,48 сантиметров.
8 Толкательные стержни, обернутые наждачной бумагой.
9 Одна-две струбцины.
10 Проволока для заклепок (проволока для сварки, гвозди, вешалки для одежды, все, что у вас есть под рукой).
Формирование клинка
Для новичка имеются два способа придать клинку форму - съем припуска и ковка. При ковке сталь клинка разогревается до пластичного состояния (900 - 1100 градусов), а затем молотком ему придается форма, близко напоминающая окончательную.
Были времена, когда все клинки были коваными. В те дни сталь дорого стоила и редко встречалась. Снятие припуска считалось непрактичным, так как при этом уничтожалось такое количество металла, из которого можно было сделать еще один или два ножа.
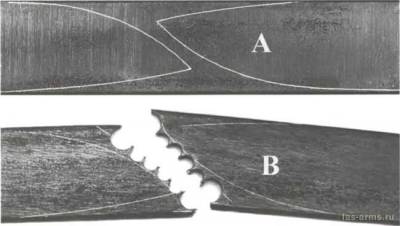
Здесь показано, как нужно просверливать и разделять стальную заготовку
Из одного и того же куска стали можно изготовить путем ковки два ножа, а путем снятия припуска — только один с полным хвостовиком. Изобретение шлифовального станка позволило быстро удалять лишнюю сталь, и данный процесс стал общепринятым при изготовлении ножей.
Хвостовик — это кусок железа, фиксированный к клинку методом кузнечной сварки. Конечно же, для тех из нас, у кого есть неограниченные запасы стали, с которой можно работать, это означает большой объем дополнительного труда.
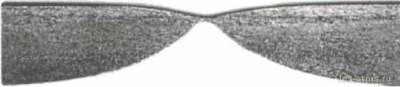
Это разделение заготовки встык при профилировании клинка.
Сварка металлолома с целью получения более крупных кусков металла была обычным делом для кузнецов, работавших на свое племя. Не следует забывать и о ветви дерева, из которой была изготовлена рукоятка, и о грубом черенке, не позволявшем рукоятке расщепиться. Отверстие в рукоятке для хвостовика точно соответствует его размерам. Это говорит о том, что хвостовик в раскаленном состоянии прожог это отверстие.
Начинающему ножовщику, который выковывает свой клинок, не нужна шлифовальная машина, если, конечно, он сможет выковать клинок близко к окончательной форме. Хорошо выкованный клинок можно доработать с помощью напильников, наждачных камней и абразивной бумаги. Это позволяет начинающему ножовщику начать свою работу по изготовлению ножей с минимальным набором инструментов.
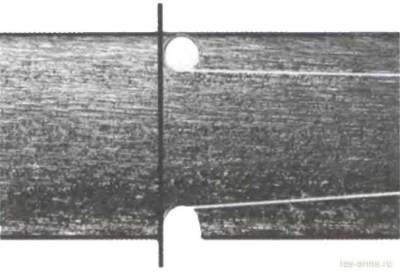
Здесь показано, как создать радиус на плече хвостовика с помощью просверленных отверстий.
Ковка хороша тем, что это процесс созидательной энергии.
Процесс съема припуска
По определению этот процесс означает: взять заготовку стали и с помощью шлифовки удалить все, что не относится к клинку. Профиль клинка выпиливается или шлифуется до нужной формы, а затем сведенный на конус профиль, представляющий собой режущую грань, шлифуется на абразивном колесе или ленте.
Стальная заготовка, выбранная для изготовления клинка методом снятия припуска, не должна быть намного толще и шире размеров предполагаемого клинка. Если вы подберете материал соответствующего размера, то сэкономите много времени на шлифовке. Для начинающего толщина клинка должна быть не более 1/8 дюйма, чтобы ему не пришлось долго заниматься его шлифовкой.
Сегодня существует тенденция изготавливать охотничьи и утилитарные ножи из стали толщиной 1/4 дюйма. Ширина клинка проектируемого ножа составляет 1 дюйм.
Профилирование клинка
Прижмите струбциной ваш шаблон к стали, просверлите два отверстия для временных заклепок, вставьте их и очертите форму клинка на стали. Отрежьте материал до нужной длины либо металлорежущей ленточной пилой, либо абразивным режущим колесом, или же отшлифуйте профиль целиком из стальной заготовки.
Еще один способ вырезать клинок из заготовки — просверлить ряд отверстий и затем сломать заготовку. Хорошо заточенное сверло легко проходит через металл. Вы скоро убедитесь, что сверлить и обламывать металл быстрее, чем пользоваться ручной ножовкой по металлу.
Другой способ отделить клинок от заготовки — начертить на ней профили двух клинков так, чтобы их концы соприкасались. Важно добиться хорошего и гладкого радиуса в том месте, где хвостовик соединяется с клинком.
После отделения клинка от заготовки металла его профиль тщательно шлифуется вплоть до начерченной линии. Для обработки профиля хорошо использовать шлифовальный станок с твердым колесом, однако наполовину засалившиеся керамические ленты, такие, как Norton SG Hogger на ленточном шлифовальном станке, удаляют лишнюю сталь раза в четыре быстрее. После процесса шлифовки скоса постоянно остаются наполовину засалившиеся ленты, которые хорошо использовать для шлифовки профиля.
Шлифовка скосов
Любой тип шлифовки клинка имеет две стадии. Первая предшествует термообработке клинка, а вторая проводится после. Лучше всего оставлять примерно 20% стали для ее удаления после термообработки. Если грани слишком тонкие, они могут коробиться или трескаться во время процесса закалки. Если же оставить немного материала для снятия после термообработки, операция по закалке будет намного безопаснее для самого клинка.
Клинки могут и действительно деформируются во время процесса закалки, и припуск материала позволит впоследствии выровнять его при шлифовке. Шлифовка до процесса термообработки не обязательно должна быть точной.
Маленькие недоделки обычно удаляются в процессе завершающей шлифовки.
Занимающийся съемом припуска ножовщик начинает с обработки прямоугольного профиля стали и придает ей форму клина. Этого можно добиться различными методами.
Шлифовка скосов на твердом колесе
Съема припуска металла можно добиться различными методами. Лучший и наиболее широко применяемый метод — работа на ленточной шлифовальной машине с использованием либо плоской платформы для клинка с плоской заточкой, либо шкива для клинка с заглубленной заточкой.
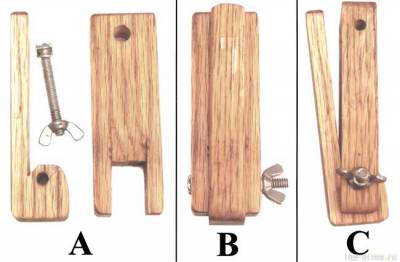
Самодельный шаблон предназначен для проверки скоса клинка.
На трех картинках показаны детали его конструкции. Его длина примерно 4 дюйма, а ширина — 1 1/2.
Важно, что само соединение вынесено отдельно, и грань клинка может полностью уходить в дно измерительного прибора
Эту же работу можно выполнить на верстачном шлифовальном станке, который иногда называют твердым колесом. Это колесо оставляет множество маленьких царапин, которые потом приходится заравнивать вручную напильником или на точильном камне, либо с помощью электроприводного плоского диска или гибкого диска.
Для аккуратной обработки скосов нужны острые новые ленты.
Причиной многих ошибок шлифовки, характерных для новичков, является использование засаленных лент. Смиритесь с тем, что каждый охотничий нож обойдется вам по крайней мере в две новые ленты. А создание ножа Боуи потребует аж пять таких лент. Если вас смущают расходы на материалы для изготовления ножей, то сейчас в самый раз пересмотреть свои планы.
Плоская шлифовка
Плоскую поверхность сравнительно легко сделать на ленточном шлифовальном станке. Выполнить это на шлифовальном колесе гораздо сложней. Чтобы сделать клин, потребуется выполнить несколько различных «дорожек», а затем их необходимо сравнять в одну поверхность стали с помощью дискового наждака или напильника.
Для разметки клинка перед каждым новым уровнем зернистости используйте красный водостойкий маркер. Для грубой обработки клинка используют ленту зернистостью 60, затем переходят на ленту зернистостью 120, чтобы достаточно отполировать его перед термической обработкой. Для контроля за ходом работы пользуйтесь OptiVISOR или другим фиксируемым на голове увеличительным стеклом. Красные чернила четко покажут любые, оставшиеся после шлифовки царапины. Проверьте наличие таких остаточных царапин при хорошем освещении.
Осмотрите клинок от острия до хвостовика, а затем — от лезвия до спинки. Плоскую шлифовку легче проводить на ленточном шлифовальном станке с плоской платформой.
Последовательность шлифовки скосов:
1 Еще раз осмотрите профиль клинка, чтоб выявить все недостатки.
2 Чтобы установить толщину грани, нанесите две линии приблизительно на расстоянии 1/32 дюйма между ними. Шлифовка до этой линии с каждой стороны позволит получить приблизительно правильную толщину грани, что обезопасит клинок во время операции по его закалке. Если скосы свести до тонкой, почти острой грани, она может потрескаться или деформироваться во время закалки.
3 На сторонах клинка пометьте место, где скосы должны закончиться. Это место иногда называют шлифовкой спуска или конечным пунктом.
4 Отшлифуйте плоский скос примерно под 45 градусов вниз к начертанной линии с каждой стороны клинка.
5 Затем отшлифуйте серию неглубоких углублений, или дорожек, по длине клинка, пока ширина скоса не определится и не станет достаточно плоской. Другой метод: по ходу работы вы можете придать клинку выпуклую форму. Используйте прямую грань для проверки хода работы либо с плоской, либо с выпуклой шлифовкой. Если шлифовка у вас не получается, потренируйтесь на более мягкой стали.
6 При шлифовке старайтесь не заходить за начертанные линии, отмечающие конечную ее точку. Также не шлифуйте слишком высоко к спинке, чтобы не сделать ее тоньше, чем хотите.
7 Отшлифуйте несколько проходов с одной стороны клинка, а затем проведите ту же работу с другой его стороны. Это позволит распределить напряжение по всему клинку более равномерно. Если снимать весь лишний материал сначала с одной стороны клинка, а затем перейти к обработке другой стороны, это может привести к деформации клинка.
8 Не делайте грань слишком тонкой до термообработки. Оставьте примерно 20% стали, которую необходимо удалить. Снимите этот припуск после того, как клинок будет закален и отпущен.
9 Соберите вместе шаблон для проверки клина клинка, изготовленный из дерева или другого материала. Укрепите этот шаблон на клинке ножа, имеющего необходимый вам клин, завинтите барашковую шайбу и поместите обрабатываемый вами клинок в измерительный прибор, чтобы определить, достаточно ли он тонок.
10 Если у вас нет ленточного шлифовального станка, используйте наждачный диск, чтобы сравнять следы, оставшиеся после шлифовального колеса. Если зернистость шлифовального колеса была 36-40, возьмите наждачный диск зернистостью 80, затем 120 и, наконец, 240. Этого будет достаточно, чтобы затем перейти к стадии термообработки. Обрежьте с диска лишний материал, это даст вам возможность обработать достаточно острые углы.
11 Вы можете обнаружить, что ваш клинок получился слегка выпуклым, но это нестрашно, если он не слишком толстый.
12 Загладьте спинку клинка или оставьте ее квадратной, но мне кажется, что последний вариант выглядит немного незаконченным. Рабочий нож получит закругленную спинку, если его сначала обработать напильником, а затем отполировать на камне с канавками.
13 С помощью тонкого камня или наждачной бумаги удалите все царапины, оставшиеся после шлифовки грани, двигая камень или наждачную бумагу от рикассо клинка (между клинком и хвостовиком) к острию и назад. Так мы удаляем любые «напряженные возвышенности», из-за которых грань может потрескаться во время закалки. Наличие грубых следов шлифовки, царапин и других неровностей можно проверить ногтем. Их называют напряженными возвышенностями. Напряжение металла, возникающее во время закалки, может привести к его растрескиванию у напряженной возвышенности, а этого следует избегать.
14 Не обрабатывайте рикассо на гибком диске. Это следует делать на тонкой ленте на плоской платформе или на гибком диске, либо вручную. Кусок влажной или сухой бумаги складывается пополам, прижимается зажимами к стальной пластине, и рикассо полируется вручную. Этот метод требует времени, но дает хорошие результаты, когда работа завершается на бумаге зернистостью 600.
15 Обязательно сделайте соединение между хвостовиком и рикассо плавно закругленным. Снова внимательно осмотрите весь клинок. Теперь он готов к термообработке.
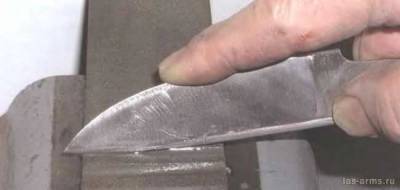
Для создания радиуса на спинке клинка используется средний камень Crystaion.
После многолетнего использования на этом камне остались заметные углубления.
Когда, изнашиваясь, углубление становится слишком широким, начните другое.
Для смазки камня используйте керосин без запаха или масло для лампы.
Работа напильником
Работа напильником относится к старой школе. Этот метод позволяет сделать поверхность исключительно плоской. Такой навык весьма полезно освоить, если у вас нет ленточного шлифовального станка. При изготовлении ножа перед термообработкой клинок делается плоским с помощью напильника. После закалки и отпуска клинок будет слишком твердым для напильника.
Напильник нужно взять за оба конца и обрабатывать деталь, двигая им вперед-назад. При этом напильник проходит вдоль всего клинка.
Если толкать напильник вперед, как принято при обычной работе, его зубцы глубже врезаются в сталь и полировка получается грубой. Для гладкой полировки лучше использовать стандартный драчовый напильник. Напильник с перекрестной насечкой снимает припуск быстрее, но оставляет небольшие возвышенности, которые следует заравнивать драчовым напильником.

Ручная обработка наждаком делает рикассо плоским и без царапин.
Влажная или сухая наждачная бумага складывается вдвое на стальной пластине.По краям бумагу удерживают пружинные зажимы.
Начните с бумаги зернистостью 80—1 20, затем все мельче и мельче, пока не добьетесь желаемой полировки.
Обычно заканчивается работа на бумаге зернистостью 600.
Таким образом, деталь можно сделать плоской и блестящей, если у вас нет машины с плоским диском.
Чтобы зубцы напильника не врезались слишком глубоко, ваши движения должны быть легкими. Всегда держите под рукой игольчатую ленту и после нескольких движений очищайте на ней зубцы напильника. Если зубцы забиваются, это может привести к истиранию поверхности и лишь добавит вам работы. Считается, что если покрыть напильник меловой пылью, это предотвратит загрязнение его зубцов. Вполне оправдано покупать хорошие качественные напильники.
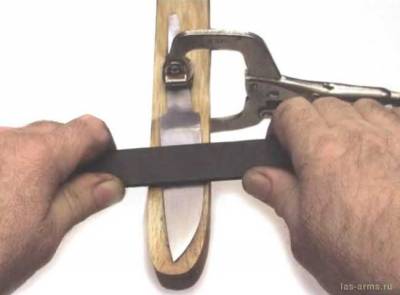
Работа напильником: для безопасности клинок прижат к поддерживающей доске.
Термообработка
Мы все знаем, что цивилизация не была бы возможной, если бы человек не научился использовать железо и сталь в той степени, как это делается сегодня. Сталь уникальна и полезна, потому что, обработав ее, сталь можно сделать исключительно твердой, пружинистой или относительно мягкой.
Будучи ножовщиками, мы можем использовать экстремальные формы термообработки, чтобы получить нужную нам сталь.
Лучшим примером этому может служить клинок, который был избирательно закален или избирательно отпущен. Такой клинок может иметь исключительно твердую грань и вместе с тем выдерживать тест на изгиб до 90 градусов. Это становится возможным, если грань ножа твердая, центральная часть клинка пружинистая, а спинка относительно мягкая.
Термообработку можно охарактеризовать как определенную, временную/температурную обработку металла для получения конкретной прочности, ковкости или других качеств. Термообработка клинка лежит в сердце любого ножа. Термообработка считается успешной, если клинок может выполнять предназначенную ему работу.
Если клинок слишком мягкий, он не сможет держать заточку и будет сильно сгибаться при тяжелой работе. Если слишком твердый — сломается даже при нормальном использовании. При правильной термообработке ножа его клинок не слишком тверд и не слишком мягок. Лучше всего определять это путем проб и ошибок, сравнивая ваши клинки с клинками из новых типов стали либо с клинками, прошедшими известную термообработку.
Любой процесс термообработки состоит из трех этапов: нагревание, остывание и время. Любое незначительное изменение температуры может значительно воздействовать на результат.
Элемент времени, возможно, наименее важен, но именно правильное сочетание времени и температуры необходимо для довершения трансформаций, приносящих нужные результаты. Каждый тип стали имеет свою собственную уникальную комбинацию циклов времени/температуры, которая позволяет получить клинок отличной прочности и режущей способности.
Способность ножа держать грань почти полностью зависит от его относительно высокой твердости. Примерно, 95% ножей, изготовленных вручную, обладают твердостью 57—61 по шкале Рокуэлла. Специфические элементы сплавов некоторых типов стали делают их более прочными по сравнению с другими типами стали той же твердости.
Предполагаемое использование ножа определяет его максимально допустимую твердость. Как правило, соответствующая термообработка более важна, чем тип стали. При правильной термообработке сравнительно простая сталь будет работать лучше, чем изысканная сталь после неправильной термообработки.
Закалка
Если сталь нагреть до определенной температуры, а затем быстро остудить, она становится твердой, хрупкой и напряженной.
Это называется закалкой. Такая форма стали известна под названием «мартенсит». Пройдя процесс закалки, мартенсит становится хрупким, напряженным и не подходит для изготовления ножа. Если нагреть мартенсит до меньшей температуры, он станет несколько мягче, выпустит напряжение, и если температура была выбрана правильно, в результате получится прочный и пригодный продукт.
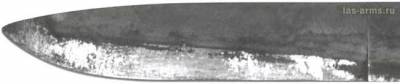
Свежезакаленный клинок.
Обработка стали при меньшей температуре, обычно между 190 и 260 градусами, называется отпуском или получением нужной степени твердости.
Источник тепла
Источник тепла для процесса закалки должен обеспечивать равномерный нагрев и возможность контролировать температуру. Если источник тепла слишком разогрет, трудно медленно и единообразно нагреть клинок. Если нагревать клинок слишком быстро или если источник тепла чересчур раскален, тонкие участки клинка, как правило, перегреваются. Газовый горн — прекрасный источник тепла для процесса закалки, если, конечно, температуру нагрева можно контролировать и регулировать.
Вот как работает газовый горн: пламя разогревает футеровку горна или печи, и радиируемое ей тепло нагревает материал. Горелка или паяльная лампа, нагревающие деталь на открытом воздухе, теряет 200% и более потенциального тепла.
Если пламя ограничивается нагревательной камерой или чем-то таким простым, как теплоулавливатель, вы сможете равномерно нагреть крупную деталь. Пламя горелки или паяльной лампы никогда не должно быть направлено непосредственно на обрабатываемую деталь. Его нужно направить так, чтобы пламя обходило саму деталь и одновременно нагревало футеровку печи.
Отпуск
Отпуск — это цикл или циклы слабого нагрева, необходимые для незначительного размягчения (отпуска) мартенсита и одновременного снятия напряжения металла, возникшего при закалке.
Окончательной формой стали в законченном клинке является отпущенный мартенсит. Отпуск клинков, изготовленных из углеродистой стали или ее сплавов, проводится при температуре 190 - 260 градусов.
В результате процесса отпуска нужно получить правильную степень твердости. Важно, чтобы клинок ножа имел мелкозернистую структуру. В результате перегрева во время ковки или нагрева для отпуска клинок может получиться слабым крупнозернистым.
Клинок с мелкозернистой структурой всегда будет превосходить по силе клинок той же твердости, но крупнозернистый.
Для отпуска только что закаленных клинков вам потребуется тостер или обычная домашняя печь. Отпуск клинка необходимо проводить незамедлительно, чтобы снять высокое напряжение мартенсита, возникшее при успешной закалке. Для этого подходит любая печь, дающая равномерный нагрев до температуры 160—260 градусов.
На полку устанавливается термометр в качестве визуального индикатора температуры. Перед тем как приступить к отпуску любых клинков, проведите следующую проверку вашей печи:
Включите ее и установите регулятор на 160 градусов; подождите 20 минут, пока температура не станет постоянной; поместите в печь только что отшлифованный кусок стали; оставьте его там на 45 минут; извлеките сталь; дайте ей остыть; посмотрите, какого она будет цвета.
Оттенок углеродистой стали должен быть чем-то средним между цветом соломы и коричневым цветом. Этот оттенок должен равномерно распределяться по всей длине стали. Такой цвет дает оксид, возникающий при нагреве, и этот оттенок является достаточно точным индикатором температуры для всех аналогичных типов стали.
Если вам покажется, что одна часть клинка нагрелась больше, чем другая, то, возможно, вам потребуется положить кусок стали между нагревательным элементом и полкой. Установите регулятор нагрева так, чтобы в результате получался цвет темной соломы или коричневый. Вы должны иметь возможность потом обработать грань напильником.
Другой метод отпуска — это использование, шаблона. Этот шаблон изготовлен из меди, но может быть сделан из нержавеющей или мягкой стали. Мягкая сталь изнашивается быстрее и не прослужит вам так долго, как медь или нержавеющая сталь. Размеры боковых медных пластин составляют 3/8 х 1 х 5 дюймов. Проем для клинка составляет четверть дюйма, либо делается настолько широким, чтобы воспринять самый толстый клинок, который вы захотите отпустить с помощью этого шаблона.
Шаблон для закалки должен быть довольно тяжелым, чтобы удерживать достаточно тепла для адекватной селективной закалки крупных клинков. Удлинение на месте прокладки для клинка необходимо для того, чтобы за него можно было держать клинок и шаблон клещами или плоскогубцами, когда вы помещаете их в горн или вынимаете из него. При определенной практике можно добиться хорошего селективного отпуска.
Попрактикуйтесь с этим перед тем, как использовать данный метод на закаленном клинке. Шаблон для отпуска должен быть довольно небольшим, чтобы помещаться в нагревательной камере кирпичной печи. Шаблон нагревается до оранжевого цвета, вынимается и помещается на огнеупорный кирпич. Спинка клинка удерживается в этом шаблоне.
Клинок следует шевелить, двигая его вперед-назад в проеме, при этом особое внимание нужно уделять рикассо. Если не проследить, то более тонкое острие может перегреться. Спинка клинка должна стать голубого цвета, а режущая грань — цвета темной соломы.
Под рукой необходимо иметь емкость с водой, чтобы остудить грань, если цвет будет слишком быстро распространяться к ней.
Грань охлаждают, быстро окуная ее в воду и вынимая. Клинок ни в коем случае не следует оставлять в воде, так как в результате термального шока могут появиться микроскопические трещины, которые погубят нож в будущем.
Отжиг
Отжиг — это процесс термообработки, в результате которого сталь становится максимально мягкой. Потом ее легче обрабатывать напильником или формировать на фрезерном или токарном станке. От поставщиков сталь обычно поступает в форме прямоугольных заготовок либо в виде горяческатной отожженной формы. Горячая скатка и отжиг являлись первым этапом процесса термообработки, и в таком виде сталь готова к обработке методом съема припуска.
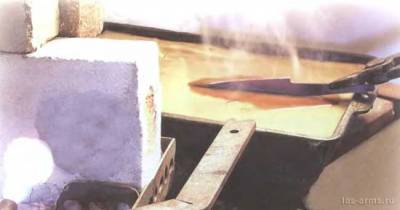
Процесс закалки грани проводится с использованием самодельной пасты в качестве закаливающего раствора.
Последовательность термообработки проектного клинка
1 Включаем печь для отпуска и ждем, когда жар станет стабильным.
2 Рядом ставим емкость с подготовленным раствором для закалки. Раскаленный клинок следует опускать в закаливающий раствор без промедления. Если вы промедлите несколько секунд, полной закалки может не получиться.
3 Разогрейте клинок для закалки в печи из одного кирпича или в другом имеющимся у вас источнике тепла. Нагревайте медленно и единообразно до тех пор, пока клинок не перестанет притягивать прислоняемый к нему магнит.
4 Быстро окуните клинок вперед острием либо в теплое масло, используя регулирующий блок, либо в кастрюлю с пастой. Постарайтесь как можно быстрее опустить грань клинка в закаливающий раствор хотя бы на полдюйма. Двугранные клинки следует погружать в масло острием вперед достаточно глубоко, чтобы клинок и хвостовик погрузились в раствор полностью.
5 Держите грань ножа в закаливающем растворе до тех пор, пока его спинка не потеряет цвет. По мере того, как паста тает, быстро вынимаем грань и окунаем ее снова в пасту. Это необходимо, чтобы охлаждение происходило постепенно.
6 Продолжайте остужать клинок до тех пор, пока не сможете взять его голыми руками.
7 Оботрите остатки раствора с клинка и проверьте его грань углом старого напильника. Процесс закалки можно считать успешным, если напильник не врезается, а просто скользит по стали. Бросьте клинок в опилки и хорошенько его очистите, а потом тщательно обработайте проволочной щеткой. Светло-серый участок свежезакаленного клинка обозначает твердую секцию. Клинок, на режущей грани которого такой цвет не проявляется, вероятно не отреагировал на процесс закалки.
8 Быстро обработайте наждаком одну сторону клинка до чистого металла и поместите его в печь для отпуска на 45 минут или час. Пусть печь продолжает работать, но клинок нужно вынуть и положить на полку, чтобы он остыл до комнатной температуры. Когда до него можно будет дотронуться рукой, поместите клинок снова в печь, по крайней мере на 45 минут еще для одного цикла отпуска.
9 Выключите печь, но клинок выньте только тогда, когда он достигнет комнатной температуры. Проверьте грань клинка напильником, которым вы пользовались ранее. Напильник должен врезаться в металл, но не слишком глубоко.
10 Завершите окончательную шлифовку клинка и проведите его проверку на латунном стержне.
Продолжение Часть 2 Смотреть |